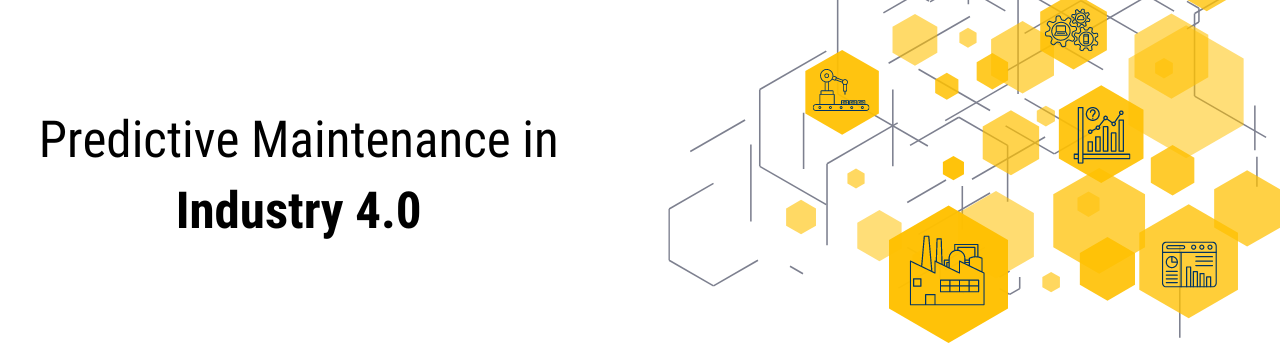
Enabling Predictive Maintenance in Industry 4.0 with MQTT and Edge Computing
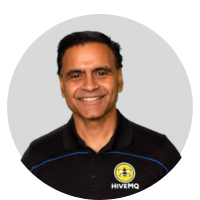
Written by Ravi Subramanyan
Category: HiveMQ Edge MQTT IIoT Edge Computing Predictive Maintenance
Published: August 31, 2023
Predictive maintenance is designed to help anticipate asset failures and allow for advanced scheduling of corrective maintenance. This prevents unexpected equipment downtime, improves service quality for customers, and reduces the additional cost caused by over-maintenance in preventative maintenance policies.
Gartner estimates that decision automation in the form of predictive maintenance will generate the highest business value for organizations with heavy assets. Businesses in asset-intensive industries struggle to maintain a balance between keeping costs down and asset availability up.
Effective asset management and maintenance play a key role in ensuring that this balance is maintained – providing these organizations with regulatory compliance, avoid unnecessary maintenance costs, and evade unplanned downtime.
Predictive maintenance techniques can be used across major industries such as oil and gas, renewables, mining industries, manufacturing industries, food and beverage industries, and others. Different types of assets including manufacturing assets, information technology assets, medical devices and more track run-time status by generating system messages, error events, and log files, which can be used to predict impending failures.
Preventive Vs. Predictive Maintenance
Preventive maintenance is planned or scheduled maintenance that takes place on a regular basis irrespective of asset conditions. This is what Maintenance Managers in manufacturing plants typically do to prevent unplanned downtime.
Predictive maintenance is performed only when it is necessary, depending on asset conditions i.e. when there is a predicted risk of equipment malfunction or failure. This uses advanced analytics.
Although the upfront investment for predictive maintenance is comparatively higher than preventive maintenance, in the long run, operational costs can be reduced by eliminating unnecessary maintenance.
How Predictive Maintenance Works?
Predictive maintenance is performed by evaluating the health and performance of assets through periodic or continuous asset condition monitoring. Data captured by IoT devices connecting different assets and systems enable businesses to predict, plan, and take proactive steps for events like parts repair or asset failure before they occur. To avoid disruption to the business, predictive maintenance is mostly performed while the equipment is operating under normal working conditions.
One common way to implement predictive maintenance is by using ML and AI techniques to get insights for machine maintenance and failure prevention. Some of the common aspects of the techniques are predicting:
- Where an equipment is in its life
- The remaining useful life (RUL) of an equipment
- The number of cycles remaining before the equipment completely breaks down.
This can be used in various industries to help with real-time monitoring of a machine’s health and correct time maintenance to reduce costs of over-maintenance.
Benefits of Predictive Maintenance
Safety, costs, and asset management are all big benefits of the investment into predictive maintenance. According to a report by PwC, on average, predictive maintenance in factories could:
- Reduce costs by 12%
- Improve uptime by 9%
- Reduce safety, health, environment, and quality risks by 14%
- Extend the lifetime of an aging asset by 20%
Industrial IoT (IIoT) Technology and Edge Power Predictive Maintenance
In industrial processes enabled by Industry 4.0 and IIoT, the assets are interconnected via IoT sensors and IoT devices. These connected industrial assets track the relevant IoT data, which can then be used to predict that a failure is about to occur. Smart IoT sensors are used throughout the industrial process to provide this information.
For example, sensors installed in remote oil wells in upstream oil and gas can observe the temperature crossing the threshold values, implying that the oil well or some part of it may fail soon. Once the data is collected through sensors, IIoT can perform analytics to predict the outcomes proactively. With visibility and real-time analytics on Industrial Edge, manufacturers can know when an asset is going to fail and how it is going to fail so they can take preventive measures to avoid downtime.
Edge computing specifically is important when decisions need to be made closer to where the action is happening. For example in some oil and gas operations with critical equipment, predicting failures and implementing maintenance based on predictive maintenance algorithms on the Edge is important. This can then be combined with predictive maintenance algorithms running on the cloud to provide a more comprehensive maintenance scheduling strategy.
Enabling Efficient Data Movement with MQTT
Embracing IIoT technology to do predictive maintenance represents a pivotal move for manufacturers seeking to maintain a competitive edge in today’s dynamic market landscape. However, the key question arises: How can industries implement data movement for IIoT in a future-proof manner, ensuring sustainable success and continuous innovation?
The answer lies in adopting the industry-standard MQTT protocol, recognized as the de facto standard for IIoT.
Industrial Data Acquisition and Aggregation using MQTT and Sparkplug
MQTT (see Figure 1) is a standard binary publish-subscribe messaging protocol designed for fast and reliable industrial assets, systems, and application data transport to enable predictive maintenance, especially under very constrained conditions. Constraints may include unreliable network connectivity, limited bandwidth, or limited battery power. MQTT is built on top of TCP/IP, which is the go-to communication protocol to interconnect network devices on the Internet. For these reasons, MQTT is ideal for IIoT and supports an event-driven architecture.
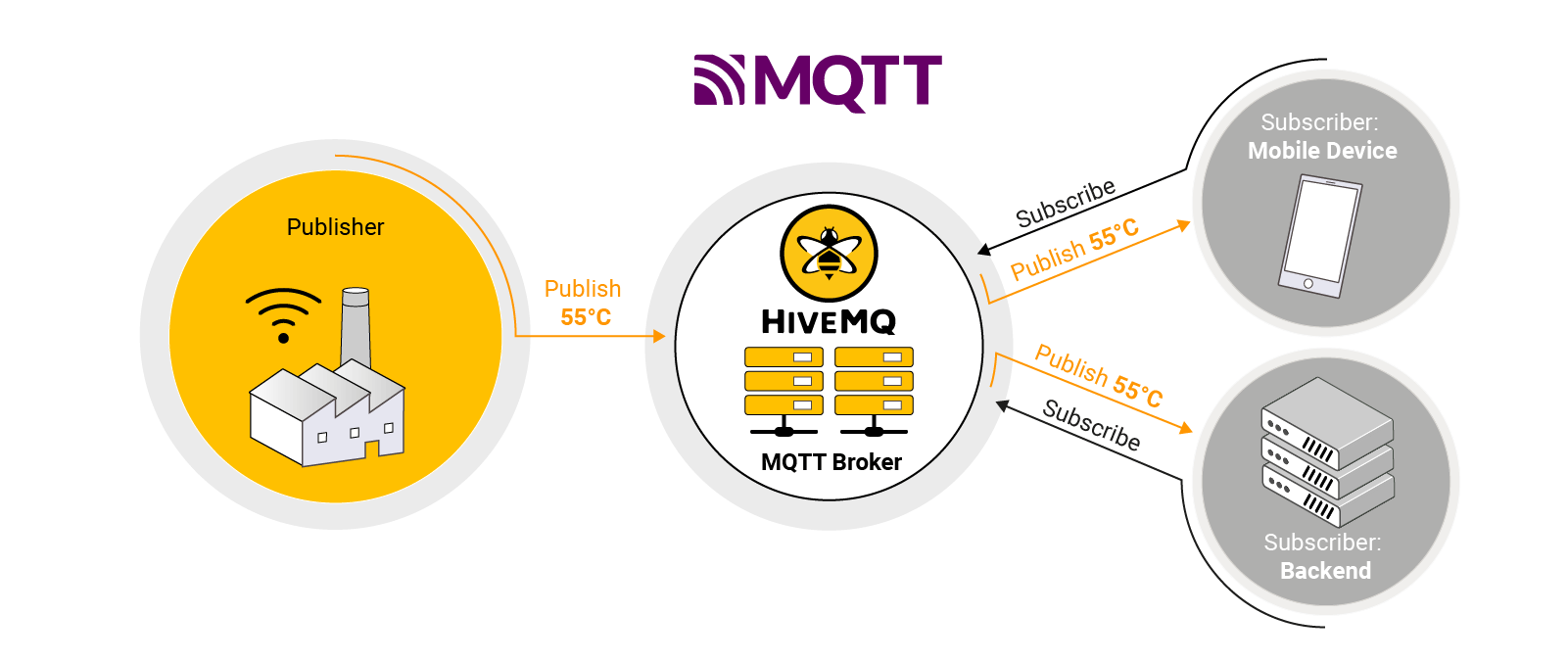
Figure 1: How an MQTT-based messaging system works
MQTT technology is designed to push data to and from thousands of remote assets, systems, and applications across the enterprise. MQTT Sparkplug is a framework that sits on top of MQTT to add more context to industrial data. It is an open-source software specification that provides MQTT clients with a framework to integrate various industrial data and provide context by defining data models. It provides a consistent way for manufacturing equipment manufacturers and software providers to share contextual factory data, enriching the predictive maintenance data.
Figure 2 provides an MQTT Sparkplug-based data architecture which shows how the data broker connects multiple machines/processes and applications to enable seamless bi-directional industrial data movement between OT and IT systems.
Figure 2: An MQTT Sparkplug-based architecture that supports multiple industrial data producers and data consumers to bridge OT to IT and enable predictive maintenance
MQTT has gained in popularity when it comes to enterprise IIoT strategy. In a survey conducted by IIoT World in 2022, MQTT was the clear winner when it came to data movement tools essential to fulfilling an IIoT strategy.
Check out the article, 5 Benefits of Using MQTT for IIoT in Tracking and Analyzing Unplanned Manufacturing Downtime, which explains the benefits that MQTT, Sparkplug and Edge Computing provide in enabling the data for use cases like Predictive Maintenance. Also, checkout Reducing Downtime with Anomaly Detection and Edge Analytics to explore how Edge Analytics and MQTT can help with predictive maintenance and reducing downtime.
Get the Data Needed for Predictive Maintenance
The MQTT protocol, along with Sparkplug, is gaining in popularity for Industrial Edge to enterprise/cloud communications as it is lightweight, reports by exception, and provides a lot of features around security, scalability, reliability, etc. MQTT is helping to drive IIoT applications that have enabled industrial process companies to enable predictive maintenance on their assets. Predictive maintenance has in turn enabled companies to reduce maintenance costs, increase asset utilization, extend asset life, and improve safety/compliance.
By seamlessly integrating IIoT with MQTT for bidirectional data movement into industrial operations, companies can trigger a paradigm shift in their processes, bolster their market position, and lay a solid data foundation for a more prosperous and efficient future.
The HiveMQ MQTT platform offers a robust bidirectional and secure MQTT communication set-up with vast integration options with technologies like Kafka, OPC UA, and more, making it one of the most preferred IoT data connectivity solutions for industrial use cases, especially predictive maintenance.
To learn more about MQTT, check out our MQTT Essentials. Or, download HiveMQ today and learn more about our fully-managed and self-managed platforms.
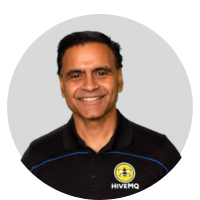
About Ravi Subramanyan
Ravi Subramanyan is a Product Marketing and Management leader with extensive experience delivering high-quality products and services that have generated revenues and cost savings of over $10B for companies such as Motorola, GE, Bosch, and Weir.
Mr. Subramanyan has successfully launched products, established branding, and created product advertisements and marketing campaigns for global and regional business teams.
Follow Ravi on LinkedIn
Exploring MQTT Sparkplug Session State Management in IIoT Communication